Volume 2 - Year 2016 - Pages 12-16
DOI: TBA
The Influence of Fiber Orientation Angle on Damping and Vibration Properties of Basalt Fiber Reinforced Composite Laminates
Ömer Yavuz Bozkurt, Özkan Özbek, Mehmet Bulut
Gaziantep University, Mechanical Engineering Department
Üniversite Blv., 27310 Şehitkamil/Gaziantep, Turkey
oybozkurt@gantep.edu.tr; ozkanozbek@gantep.edu.tr; mbulut@gantep.edu.tr
Abstract - Damping and vibration characteristics of basalt/epoxy fiber-reinforced composite laminated materials have been investigated with respect to the effect of fiber orientations. Four different symmetric laminates having [(0/90)4]S, [(15/-75)4]S, [(30/-60)4]S and [(45/-45)4]S fiber orientation angles were prepared using plain weave basalt fabrics as reinforcement. The dynamic modal analysis was performed to determine dynamic characteristics of the composite laminates. By using half power band-width method, the damping properties were deduced from vibration response envelope curve. Loss modulus, storage modulus and damping ratio of the structures were also determined. It was observed that damping and vibration characteristics of the composite samples were strongly affected by the fiber orientation of basalt/epoxy composite. The increase in angle of fiber orientation from 0˚ to 45˚ resulted in a decrease in natural frequencies and an increase in damping ratios.
Keywords: Damping, Vibration, Basalt, Composite
© Copyright 2016 Authors - This is an Open Access article published under the Creative Commons Attribution License terms. Unrestricted use, distribution, and reproduction in any medium are permitted, provided the original work is properly cited.
Date Received: 2015-06-23
Date Accepted: 2016-06-04
Date Published: 2016-11-14
1. Introduction
The protection of civil engineering structures from the dynamic loadings as like earthquake, extreme waves and highway loading has emerged the importance of structural controlling. Elimination of vibrations from the dynamic loadings can save human lives, and the vibration controlling of civil engineering structures during the earthquake is a good example for this.
In recent years, because of their improved and better characteristics, the use of the fiber reinforced composite laminated materials have extensively increased in structural applications in civil, aerospace and automotive industries. The properties of fiber-reinforced composite materials depend on several parameters such as material of fiber and matrix, curing process, fiber orientation, stacking sequence, inherent lamina and laminate level flaws introduced during the manufacturing process. Nevertheless, fibers are the primary factors controlling the properties of fiber-reinforced composite materials. Due to this, there have been a continual effort to use new stiff, strong, lightweight, low-cost and eco-friendly fibers in composite materials.
One of the exciting new fiber materials is basalt fiber. Basalt fiber is an eco-friendly material obtained from basalt. With its unique properties, basalt fiber is qualifies as a material for the production of fiber reinforced polymer composites. Over the years, several studies have been dedicated to the determination of mechanical properties of the basalt fiber reinforced composite materials. Fiore et al. [1] explored the mechanical, chemical and thermal performance of basalt fiber reinforced composite laminates. Czigány [2] investigated the contribution of basalt fibers on mechanical behaviours of hybrid fiber reinforced polyethylene composites. Lopresto et al. [3] presented the mechanical performance comparisons of plastic composites reinforced with basalt fiber and glass fiber. Cao et al. [4] presented the tensile properties of hybrid carbon/glass and hybrid carbon/basalt composites at different temperatures to show the thermal performance of the composites. Ary Subagia et al. [5] studied the effect of stacking sequences on the flexural properties of hybrid basalt/carbon composite laminates. Petrucci et al. [6] studied mechanical performance of different hybrid laminates based on basalt fiber for inner core material, and glass, flax and hemp fiber for outer layers for symmetrical configuration. Sarasini et al. [7] investigated the quasi-static mechanical properties and low velocity impact behaviour of carbon/basalt laminates and the effects of hybridization on those properties. Petrucci et al. [8] examined the impact and flexural post-impact behavior of ternary hybrid composites based on epoxy resin reinforced with basalt, flex, hemp and glass fibers. Dorigato and Pegoretti [9] investigated the hybridization effect on the flexural and impact properties of carbon/basalt fiber reinforced composite laminates. All these studies have reported the tensile, compressive, flexural, impact and thermal properties of basalt fiber reinforced composite laminates.
Damping capacity which measures the ability of vibration energy absorption is another unique characteristic of fiber-reinforced composites. It is used for reducing the transmission of noise and vibrations to neighbouring structures [10]. Several researchers studied dynamic behavior of hybrid composite laminates investigating hybridization effects. Vannan and Vizhian [11] investigated the effect of temperature on damping characteristics of aluminium alloy/basalt short fiber metal matrix composites containing various amounts of short fibers. An increase in loss modulus and damping capacity, and a decrease in storage modulus were reported with increasing temperature. It was also reported that increase in short basalt fiber contents increased both the loss modulus and storage modulus. Yan et al. [12] investigated stability dynamic response of basalt woven composite laminates. They concluded that the magnitude and phase behaviour of basalt fiber composites were quite different under the quasi-static and high strain rate loading conditions. Baştürk et al. [13] analysed nonlinear damped vibration response of a Kevlar/E-glass hybrid composite plates subjected to the blast load. The role of amplitude of the damping ratio on the deflection and the frequencies of the plate were noticed.
Based on the above literature study, the characteristics of basalt fiber reinforced composite laminates under impact, tensile and compressive loading have been investigated by several researchers. To the authors’ knowledge, there is only one open literature available on damping and vibration characteristics of basalt fiber reinforced epoxy composite. The goal of the current study is to determine the damping and vibration behaviour of basalt/epoxy composite laminates, and the evaluation of the effect of fiber orientations on the damping and vibration characteristics.
2. Materials and Methods
Plain weave basalt fiber with areal density of 200 g/m2 were used as reinforcement in the lamina. Epoxy resin (MOMENTIVE-MGS L285) with hardener (MOMENTIVE-MGS L285) in the ratio of 100:40 was used in the common matrix. Four symmetrical laminates having [(0/90)4]S, [(15/-75)4]S, [(30/-60)4]S and [(45/-45)4]S fiber angles were prepared to study the effects of fiber orientation (Table 1). The fiber volume fractions of laminates were the same in all specimens and were approximately equal to 56 %. Laminated fabrics with dimensions of 300 mm × 300 mm were prepared using vacuum assisted resin transfer molding technique. The vacuum applied was 700 mm Hg for 8 h. Then, the composite laminates were left to a post cure period at room temperature. Thickness of the composite laminates were measured as t=1.7±0.02 mm.
Table 1. Configurations of produced specimens having symmetrical stacking sequences.
Symmetrical configurations | Naming |
[(0/90)4]S | (B8)0 |
[(15/-75)4]S | (B8)15 |
[(30/-60)4]S | (B8)30 |
[(45/-45)4]S | (B8)45 |
2.1. Vibration Tests
Dynamic characteristics of composite laminates were measured using an experimental set-up according to ASTM E756 [14] as shown in Fig. 1. A general purpose PCB 352C03 ceramic shear ICP ® accelerometer for output signal acquisition, a PCB 086C03 general purpose modal impact hammer for stimulus force signal and a National Instrument product NI 9234 data acquisition device with LABVIEW software were used in the experiments. The coupons with dimensions of 200 mm ×20 mm were cut from the composite laminates using CNC router, and samples were clamped by supports (Fig. 1 (c)).
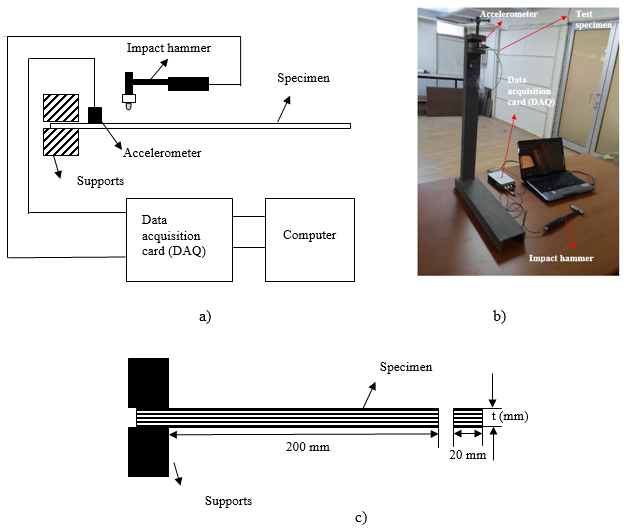
To achieve dynamic characteristics, the prepared composite samples were excited using the impact hammer. Time dependent acceleration response of the specimen was measured by the applying the impact hammer and recording the acceleration. Fast Fourier Transform (FFT) was applied to determine the magnitude versus frequency depended responses. Frequency responses were extracted within the constant frequency range from 0 to 800 Hz. Five specimens were prepared for each laminate configuration and three vibration tests were recorded for each specimen.
2.2. Damping Ratios
In order to measure damping responses, half power band-width method was used for first natural frequency mode of the specimen. The damping ratio was measured according to the half-bandwidth method as shown in Fig. 2, according to Eq. (1).

where are the bandwidth,
is the natural frequency of first mode, and
is the
damping ratio. The storage modulus
of samples was obtained using Eq. (2).
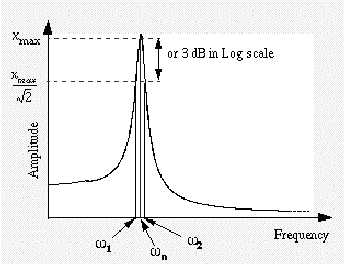
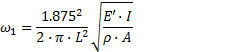
where is density
of the beam,
is the
cross-section of the beam,
is the
moment of inertia of the given cross-section of beam,
is the storage modulus,
is the free
length of the beam and
is the natural frequency of first mode.
Similarly, loss modulus
of the beam can be found using the following
relationship between loss and storage modulus.

3. Results and Discussions
From the vibration test results, the frequency response curves were plotted as shown in Fig. 3. The first and second mode natural frequency values are given in Table 2. It is observed that first mode natural frequency is clearly dominant for all samples. The natural frequency decreased with increasing fiber angle. This is explained by the alignment of fibers in the lamina which contributes to the stiffness of the specimens. In addition, while the fiber angle increases from 0˚ to 45˚, stiffness of the specimen along the longitudinal direction decreases. Due to this reason, reduction of stiffness resulted in decrease of natural frequency based on equation (2). However, damping ratio increases while fiber angle increases from 0˚ to 45. This may be attributed the reduction of vibration energy dissipation along the longitudinal direction. Similarly, Liang et al. [16] indicated that the increase of effective damping could be cause a reduction of energy dissipated and responses by means of amplitudes.
Table 2. Damping and natural frequency values.
Fiber angle | First mode (Hz) | A1 (g/N) | Second mode (Hz) | A2 (g/N) | Damping ratio | Storage modulus (GPa) | Loss modulus (GPa) |
0˚/90˚ | 33.79/td> | 89.21 | 199.68 | 118.06 | 0.348 | 18.8 | 13.1 |
15˚/-75˚ | 30.72 | 96.84 | 177.15 | 116.47 | 0.390 | 14.3 | 11.2 |
30˚/-60˚ | 28.67 | 87.36 | 169.98 | 109.00 | 0.408 | 11.6 | 9.4 |
45˚/-45˚ | 26.62 | 81.22 | 163.84 | 116.90 | 0.473 | 9.6 | 9.1 |
A1: Maximum Amplitude of First Mode; A2: Maximum Amplitude of Second Mode.
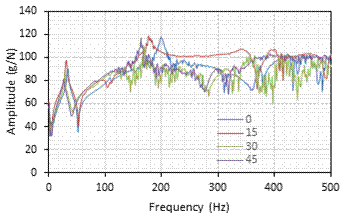
Fig. 4 illustrates the influence of fiber angle resulting from the displacement versus time records. Amplitude-time decaying curves were recorded within the same time interval (2 seconds) in order to compare damping properties of samples. It can be concluded that the increase of fiber angle of basalt-epoxy composite laminates from 0˚ to 45˚ decreased the natural frequency while increasing the damping ratios.
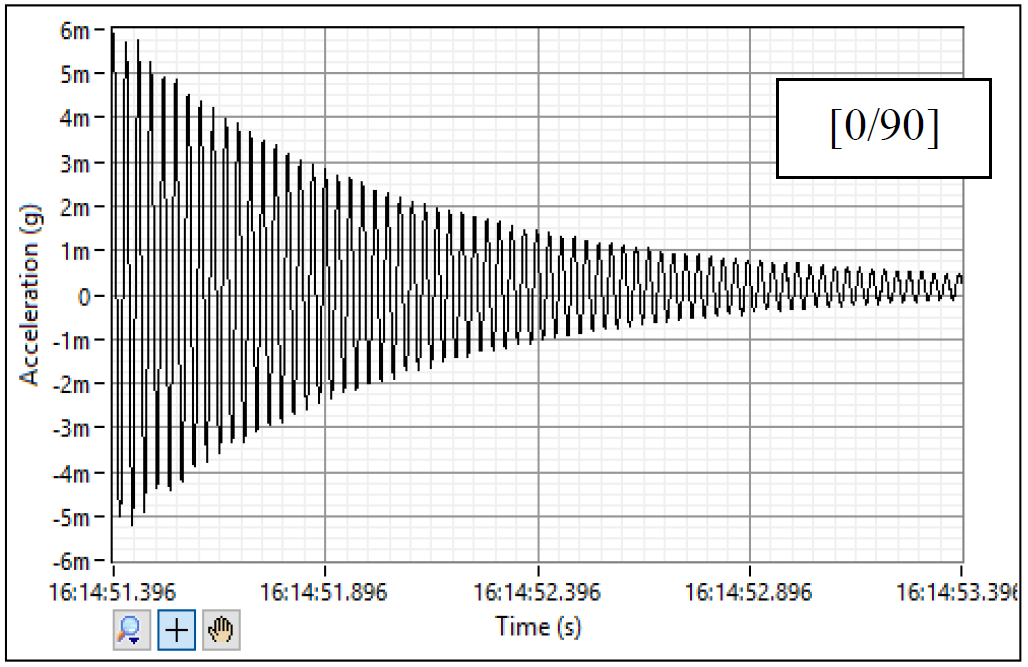
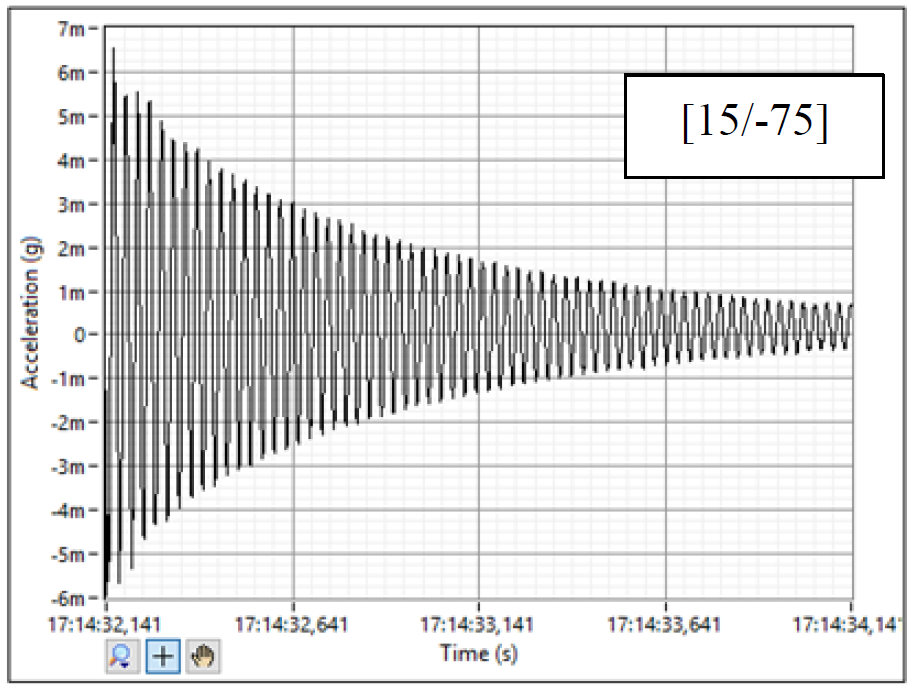
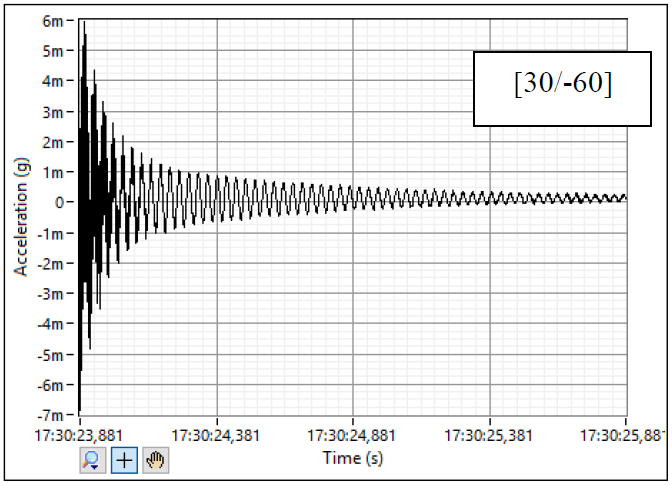
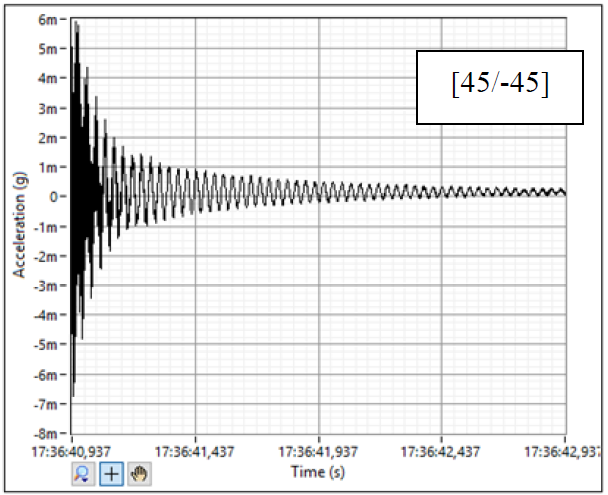
4. Conclusion
Damping and vibration characteristics of basalt/epoxy composite laminates were determined and the effect of fiber orientation was evaluated. Using the logarithmic decrement method, the damping properties were obtained from vibration response envelope curves. The main conclusions from this study can be summarized as follows:
- damping and vibration characteristics of the composite samples are strongly affected by the fiber orientation of basalt/epoxy,
- the increase in angle of fiber orientation from 0˚ to 45˚ resulted in a decrease in natural frequency,
- the laminates having higher fiber orientation angle had higher damping ratios,
- the storage and loss moduli decrease with increasing fiber orientation angle,
Finally, the results suggest that it can be possible to obtain a desired damping and vibration capability by altering the orientation angles of basalt fibers.
References
[1] V. Fiore, T. Scalici, G. Bella and A. Valenza, "A review on basalt fiber and its composites," Composites Part B, vol. 74, pp. 74-94, 2015. View Article
[2] T. Czigany, "Special manufacturing and characteristics of basalt fiber reinforced hybrid polypropylene composites: Mechanical properties and acoustic emission study," Composite Science and Technology, vol. 66, pp. 3210-3220, 2006. View Article
[3] V. Lopresto, C. Leone and I. Iorio, "Mechanical characterisation of basalt fiber reinforced plastic," Composites Part B: Engineering, vol. 42, pp. 717-723, 2011. View Article
[4] S. Cao, Z. Wu and X. Wang, "Tensile properties of CFRP and hybrid FRP composites at elevated temperature," Journal of Composite Materials, vol. 43, pp. 315-330, 2009. View Article
[5] I. Ary Subagia, Y. Kim, L. Tijing, C. Kim and H. Shon, "Effect of stacking sequence on the flexural properties of hybrid composites reinforced with carbon and basalt fibers” Compos B Eng, vol. 58, pp. 251-258, 2014. View Article
[6] R. Petrucci, C. Santulli, D. Puglia, F. Sarasini, L. Torre and J. Kenny, "Mechanical characterisation of hybrid composite laminates based on basalt fibers in combination with flax, hemp and glass fibers manufactured by vacuum infusion," Materials & Design, vol. 49, p. 728–735, 2013. View Article
[7] F. Sarasin, F. Tirillò, L. Ferrante, M. Valente, T. Valente, L. Lampani, P. Gaudenzi and S. Cioffi, "Drop-weight impact behaviour of woven hybrid basalt–carbon/epoxy composites," Composites Part B: Engineering, vol. 59, pp. 204-220, 2014. View Article
[8] R. Petrucci, C. Santulli, D. Puglia, E. Nisini, F. Sarasini, J. Tirillò, L. Torre, G. Minak and J. Kenny, "Impact and post-impact damage characterisation of hybrid composite laminates based on basalt fibres in combination with flax, hemp and glass fibres manufactured by vacuum infusion," Composites Part B: Engineering, vol. 69, pp. 507-515, 2015. View Article
[9] A. Dorigato and A. Pegoretti, "Flexural and impact behaviour of carbon/basalt fibers hybrid laminates," Journal of Composite Materials, vol. 48, pp. 1121-1130, 2014. View Article
[10] S. Adali and V. Verijenko, "Optimum stacking sequence design of symmetric hybrid laminates undergoing free vibrations," Composite Structures, vol. 54, pp. 131-138, 2001. View Article
[11] R. Karthigeyan, S. Vannan and S. Vizhian, "Investigation on the Influence of Basalt Fiber on Thermal properties of Al7075/ Basalt Fiber Metal Matrix Composites," Procedia Engineering, vol. 97, pp. 432-438, 2014. View Article
[12] J. Yan, B. Gu and B. Sun, "Dynamic response and stability of basalt woven fabric composites under impulsive compression," Journal of Reinforced Plastics and Composites, vol. 32, pp. 137-144, 2013. View Article
[13] S. Baştürk, H. Uyanık and Z. Kazancı, "Nonlinear damped vibrations of a hybrid laminated composite plate subjected to blast load," Procedia Engineering, vol. 88, pp. 18-25, 2014. View Article
[14] ASTM, “ASTM E756 - Standard Test Methods for Measuring Vibration Damping Properties of Materials,” 2010. View Document
[15] I. Saidi, N. Haritos, E. Gad and J. Wilson, "Floor vibrations due to human excitation-damping perspective," Earthquake Engineering in Australia, Canberra, pp. 24-26, 2006. View Article
[16] Z. Liang, G. Lee, L. Dargush and J. Song, Structural Damping, Applications in Seismic Response Modification, Boca Raton: CRC Press, 2012. View Book